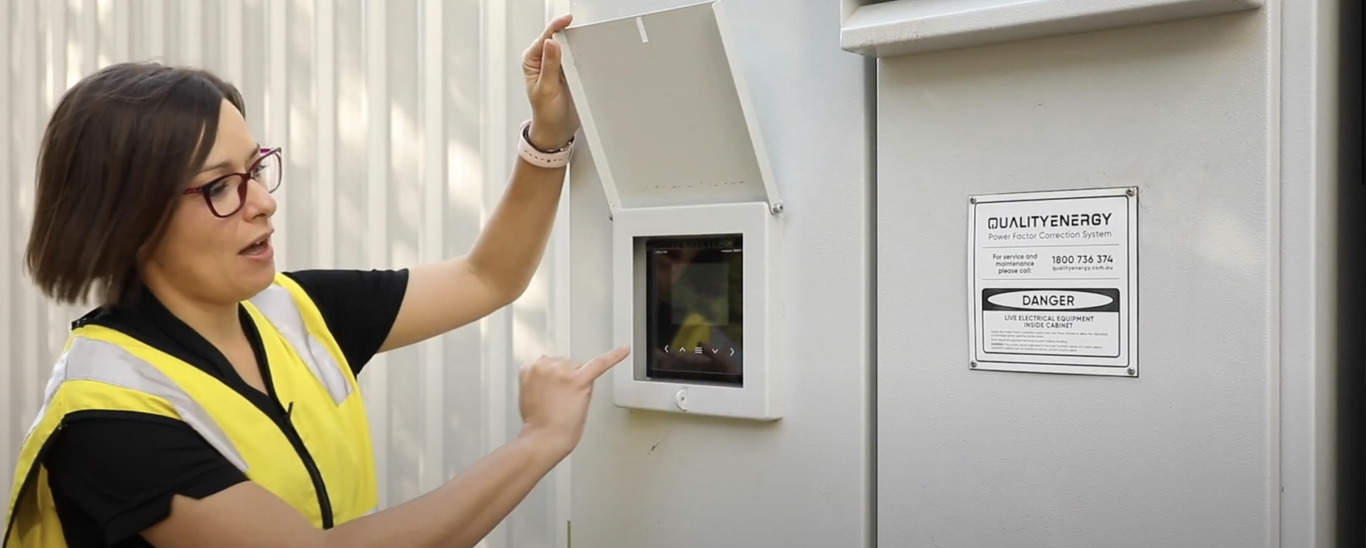
Momentum is a vital ingredient in making environmental sustainability a part of a company’s culture, as two of South Australia’s leading wine industry businesses can attest.
Dorrien Estate Winery and contract packaging and distribution company Vinpac International have made huge strides in little more than two years, empowered by the commitment of their parent company Woolworths and supported by Green Industries SA (GISA).
Central to this has been a determination not only to do things better across their facilities in the Barossa Valley and McLaren Vale, but to actively contribute to the circular economy by thinking about what happens to their waste further down the line.
Both businesses have had strong green credentials for many years, but things really came together in August 2017 when it was decided that Dorrien Estate’s inhouse Environmental and Quality Systems Specialist, Laura Herrero-Chorques, should formally turn her attention to Vinpac’s environmental needs as well.
One of her first steps was to take advantage of the South Australian Government Trade Waste Initiative, which provided funding towards a comprehensive activity audit and assessment around energy and waste water.
“I thought that would be a very good starting point for us because we hadn’t done a proper energy audit in previous years: certainly not anything that was totally independent,” she said.
“In order for me to be able to develop a strategy and a plan to improve the efficiency of our sites we needed to know where we were – to have some benchmarking.”
Detailed work by third-party consultants produced separate recommendations for the two businesses, but there were common themes, and Woolworths is progressing on implementing a number of initiatives.
New solar electricity systems are top of the agenda. A 1-megawatt system at Vinpac’s Barossa site (where activities include winemaking, bottling and cellar management) will bring expected savings of around $240,000 a year, while a 400-kilowatt system at Dorrien Estate will cut costs by about $120,000. Simple payoff is expected in just six or seven years.
In addition, all lights at Dorrien Estate have been switched to more efficient LED, with Vinpac to follow. Expected annual savings will be $24,300 and $99,000 respectively, with both systems expected to be paid off in little more than two years once operational.
Having invested its own time and money in the audit, Dorrien Estate was eligible for an efficiency implementation grant from the Department of Energy and Mining, which funded 50% of the cost of installing power factor correction equipment. As a result, the winery’s own equipment works more effectively and efficiently, with expected annual savings of more than $20,000.
“The Green Industries SA support and the access it gave us to the other grant was really important not just in financial terms but also in helping us develop our strategies and make internal decisions,” Laura said.
More was to follow, this time with the focus on solid waste and recycling. Through the GISA Business Sustainability Program, a baseline study was undertaken which put some hard numbers around how the two businesses are performing and how they can improve.
The upfront news was very good. They are responsibly disposing of 99% of waste rather than just adding it to landfill, and because their systems for segregating different types of waste are so effective, they make a nett profit from recycling through their ability to access rebates for glass, cardboard and plastic.
“Our people didn’t know this, so it was very important for awareness and morale,” Laura said. “All the teams on site are doing a very good job and they are now inspired to do even better.”
Doing better means embracing the circular economy and understanding the concept of a waste hierarchy, which ranks various tiers of waste disposal and provides scores and targets for individual operations.
“For example, we currently don’t send any waste to landfill because our contractor uses general waste for energy recovery – they produce energy by burning waste – but in the waste hierarchy, burning waste is only just above landfill,” Laura said.
“What we want to do now is start recycling before burning. Once you burn it, material is not in the system anymore; the aim is to actually bring those materials back to the highest values they can have.”
Stage two of this project, again supported by GISA, will include assessments of Vinpac’s other bottling facilities in McLaren Vale and the Gawler Belt.
Laura’s aim – supported by Woolworths – is to have key sites achieve ISO 14001 Environmental Management certification.
“The real change in the past few years is that waste, recycling and energy management are on the agenda for discussion internally and the support and encouragement from Green Industries has been a big part of that,” she said.
“Having access to consultants and to other expertise has allowed us to really get things moving and achieve results in months rather than years.
“Everyone has been doing a good job as we now can see, we have good systems in place and have been managing our systems well, but now we can put a name to processes. And employees see that management is committed.”